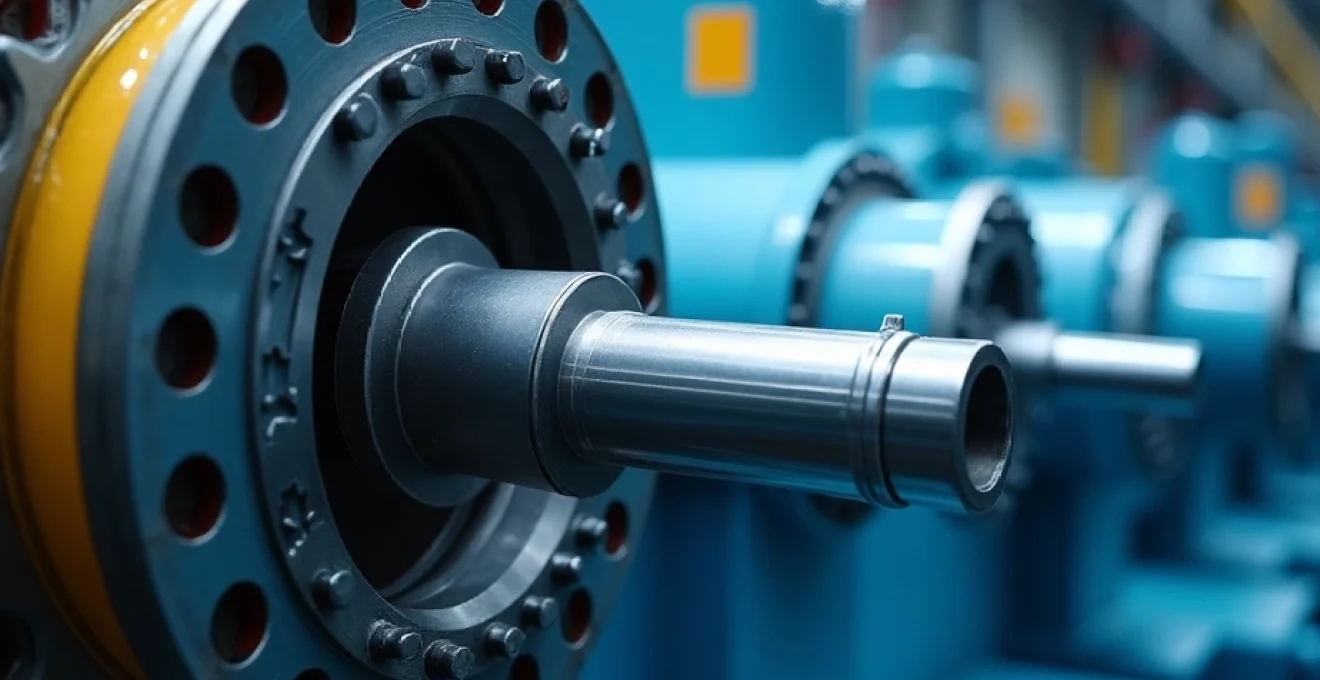
En el mundo industrial y empresarial, la eficiencia operativa es fundamental para el éxito. Un factor crítico que a menudo se pasa por alto es el mantenimiento preventivo de equipos y maquinaria. Esta estrategia proactiva no solo extiende la vida útil de los activos, sino que también previene costosas interrupciones y reparaciones de emergencia. Al anticiparse a los problemas potenciales, las organizaciones pueden optimizar su rendimiento, reducir costos operativos y mejorar la seguridad en el lugar de trabajo. ¿Pero cómo se implementa efectivamente un programa de mantenimiento preventivo y cuáles son sus beneficios reales?
Fundamentos del mantenimiento preventivo en sistemas mecánicos
El mantenimiento preventivo se basa en la premisa de que es más eficiente y económico prevenir fallos que repararlos después de que ocurran. Este enfoque implica la realización de inspecciones regulares, limpieza, lubricación y reemplazo de componentes desgastados antes de que fallen. Para los sistemas mecánicos, esto puede incluir tareas como el análisis de vibraciones, la alineación de ejes, la verificación de niveles de aceite y la inspección visual de piezas críticas.
Un aspecto fundamental del mantenimiento preventivo es la planificación sistemática. Esto implica crear un calendario detallado de tareas de mantenimiento basado en las recomendaciones del fabricante, el historial de rendimiento del equipo y las condiciones operativas específicas. Por ejemplo, una máquina que opera en un entorno polvoriento puede requerir limpieza y lubricación más frecuentes que una que funciona en un ambiente controlado.
Otro componente clave es el registro meticuloso de todas las actividades de mantenimiento. Estos registros proporcionan una valiosa fuente de datos para analizar tendencias, predecir fallos futuros y optimizar los intervalos de mantenimiento. Además, ayudan a cumplir con los requisitos regulatorios y de seguridad en muchas industrias.
La implementación efectiva del mantenimiento preventivo puede reducir los costos de mantenimiento hasta en un 30% y aumentar la disponibilidad de los equipos en más del 90%.
Técnicas avanzadas de diagnóstico para detección temprana de fallas
Las técnicas de diagnóstico avanzadas son esenciales para un mantenimiento preventivo efectivo. Estas herramientas permiten a los técnicos identificar problemas potenciales mucho antes de que se conviertan en fallas costosas. Al utilizar estas técnicas, las empresas pueden pasar de un enfoque reactivo a uno proactivo en el mantenimiento de sus activos críticos.
Análisis de vibraciones en maquinaria rotativa
El análisis de vibraciones es una técnica poderosa para detectar problemas en equipos rotativos como motores, bombas y turbinas. Al medir y analizar los patrones de vibración, los técnicos pueden identificar desalineaciones, desequilibrios, desgaste de rodamientos y otros problemas mecánicos en sus etapas iniciales. Esta técnica es particularmente valiosa porque permite el diagnóstico sin necesidad de desmontar el equipo, lo que ahorra tiempo y recursos.
La implementación del análisis de vibraciones implica el uso de sensores especializados y software de análisis. Los datos recopilados se comparan con líneas base establecidas para detectar anomalías. Por ejemplo, un aumento en la amplitud de vibración a ciertas frecuencias puede indicar un rodamiento desgastado, mientras que vibraciones a la frecuencia de rotación del eje podrían sugerir un problema de equilibrio.
Termografía infrarroja para identificación de puntos calientes
La termografía infrarroja utiliza cámaras especiales para capturar imágenes de calor emitido por los equipos. Esta técnica es invaluable para detectar problemas eléctricos, mecánicos y de aislamiento. Los puntos calientes anormales pueden indicar conexiones eléctricas sueltas, fricción excesiva en componentes mecánicos o fugas en sistemas de aislamiento térmico.
La belleza de la termografía radica en su capacidad para proporcionar una imagen visual clara de problemas que de otro modo serían invisibles. Por ejemplo, un panel eléctrico que muestra un punto caliente en una imagen térmica podría indicar un disyuntor sobrecargado o una conexión suelta, permitiendo a los técnicos abordar el problema antes de que ocurra un fallo catastrófico.
Monitoreo de aceite y análisis de partículas metálicas
El análisis de aceite es como realizar un "examen de sangre" a una máquina. Al examinar muestras de aceite de motores, transmisiones y sistemas hidráulicos, los técnicos pueden obtener información valiosa sobre la salud interna del equipo. Este análisis puede revelar la presencia de contaminantes, la degradación del aceite y, lo más importante, partículas metálicas que indican desgaste de componentes.
El monitoreo regular del aceite puede ayudar a:
- Detectar desgaste prematuro de componentes
- Optimizar los intervalos de cambio de aceite
- Identificar problemas de contaminación
- Prevenir fallas catastróficas de equipos
Ultrasonido para detección de fugas y desgaste prematuro
La tecnología de ultrasonido se utiliza para detectar sonidos de alta frecuencia producidos por equipos en funcionamiento. Es particularmente útil para identificar fugas en sistemas de aire comprimido, vapor o vacío, así como para detectar desgaste prematuro en rodamientos y otros componentes mecánicos.
Los detectores de ultrasonido pueden captar sonidos que están fuera del rango audible humano, permitiendo a los técnicos localizar problemas que de otro modo pasarían desapercibidos. Por ejemplo, una fuga de aire comprimido puede ser inaudible para el oído humano, pero fácilmente detectable con un dispositivo de ultrasonido, lo que permite reparaciones rápidas y ahorro de energía.
Implementación de programas de mantenimiento predictivo
La transición de un mantenimiento reactivo a uno predictivo requiere un enfoque sistemático y un cambio cultural en la organización. El mantenimiento predictivo va un paso más allá del preventivo, utilizando datos y análisis avanzados para predecir cuándo es probable que ocurra un fallo y programar el mantenimiento solo cuando es necesario.
Desarrollo de indicadores clave de rendimiento (KPIs) de mantenimiento
Los KPIs son fundamentales para medir la efectividad de un programa de mantenimiento predictivo. Algunos indicadores críticos incluyen:
- Tiempo medio entre fallos (MTBF)
- Tiempo medio de reparación (MTTR)
- Disponibilidad general del equipo (OEE)
- Costo de mantenimiento por unidad de producción
- Porcentaje de mantenimiento planificado vs. no planificado
Estos KPIs proporcionan una visión clara del rendimiento del programa de mantenimiento y ayudan a identificar áreas de mejora. Por ejemplo, un aumento en el MTBF indica que los equipos están operando por períodos más largos sin fallos, lo que sugiere un mantenimiento efectivo.
Integración de sistemas CMMS (computerized maintenance management system)
Un CMMS
es el corazón de un programa de mantenimiento predictivo efectivo. Estos sistemas ayudan a gestionar todos los aspectos del mantenimiento, desde la programación de tareas hasta el seguimiento de inventario de repuestos. La integración de un CMMS permite:
- Automatizar la programación de tareas de mantenimiento
- Centralizar los registros de mantenimiento y reparaciones
- Analizar tendencias de fallas y costos
- Optimizar la gestión de inventario de repuestos
- Generar informes detallados para la toma de decisiones
Planificación de rutinas de inspección basadas en criticidad de equipos
No todos los equipos son igualmente críticos para las operaciones. La planificación de rutinas de inspección debe basarse en un análisis de criticidad que considere factores como el impacto en la producción, los costos de reparación y los riesgos de seguridad. Los equipos más críticos requerirán inspecciones más frecuentes y detalladas, mientras que los menos críticos pueden tener intervalos de inspección más largos.
Por ejemplo, en una planta de producción, una prensa hidráulica principal puede requerir inspecciones semanales detalladas, mientras que un sistema de ventilación secundario podría inspeccionarse mensualmente. Esta priorización asegura que los recursos de mantenimiento se utilicen de manera más eficiente.
Capacitación del personal en técnicas de mantenimiento proactivo
El éxito de un programa de mantenimiento predictivo depende en gran medida de la habilidad y conocimiento del personal de mantenimiento. La capacitación continua es esencial para mantenerse al día con las últimas técnicas y tecnologías. Esto puede incluir:
- Formación en el uso de equipos de diagnóstico avanzados
- Cursos sobre análisis de datos y tendencias
- Entrenamiento en metodologías de resolución de problemas
- Certificaciones en técnicas específicas como análisis de vibraciones o termografía
Optimización de costos mediante mantenimiento preventivo
La implementación efectiva de un programa de mantenimiento preventivo puede llevar a una significativa optimización de costos en varios frentes. Desde la reducción de tiempos de inactividad no planificados hasta la extensión de la vida útil de los equipos, los beneficios financieros son sustanciales y multifacéticos.
Análisis de ciclo de vida útil de componentes críticos
El análisis del ciclo de vida útil de los componentes críticos es fundamental para optimizar los costos de mantenimiento. Este enfoque implica estudiar el patrón de desgaste y fallo de componentes específicos a lo largo del tiempo. Al comprender estos patrones, las organizaciones pueden tomar decisiones informadas sobre cuándo reemplazar componentes para maximizar su vida útil sin arriesgar fallos catastróficos.
Por ejemplo, en una turbina eólica, el análisis del ciclo de vida de los rodamientos principales puede revelar que, aunque su vida útil esperada es de 10 años, reemplazarlos preventivamente a los 8 años reduce significativamente el riesgo de fallo y los costos asociados de reparación de emergencia y tiempo de inactividad.
Estrategias de reemplazo programado vs. mantenimiento correctivo
La decisión entre el reemplazo programado y el mantenimiento correctivo debe basarse en un análisis costo-beneficio detallado. Mientras que el mantenimiento correctivo puede parecer más económico a corto plazo, a menudo resulta más costoso cuando se consideran los tiempos de inactividad no planificados y los daños colaterales.
Una estrategia de reemplazo programado, basada en datos de rendimiento y análisis predictivo, puede:
- Reducir los tiempos de inactividad no planificados
- Minimizar el impacto en la producción
- Permitir una mejor planificación de recursos y presupuesto
- Extender la vida útil general del equipo
Gestión de inventario de repuestos y optimización de stock
Una gestión eficiente del inventario de repuestos es crucial para optimizar los costos de mantenimiento. Mantener un equilibrio entre tener suficientes repuestos para evitar tiempos de inactividad y no sobrecargar el inventario con piezas innecesarias es un desafío constante.
La implementación de un sistema de gestión de inventario integrado con el CMMS puede ayudar a:
- Predecir las necesidades de repuestos basadas en datos históricos y programas de mantenimiento
- Automatizar los pedidos de reposición
- Identificar piezas obsoletas o de baja rotación
- Optimizar los niveles de stock para diferentes categorías de repuestos
Tendencias futuras en mantenimiento preventivo y predictivo
El campo del mantenimiento industrial está evolucionando rápidamente, impulsado por avances tecnológicos y la creciente necesidad de eficiencia operativa. Las tendencias emergentes están redefiniendo cómo las empresas abordan el mantenimiento de sus activos críticos.
Integración de IoT y análisis de datos en tiempo real
La Internet de las Cosas (IoT) está transformando el mantenimiento preventivo al permitir la recopilación continua de datos de equipos en tiempo real. Los sensores integrados en la maquinaria pueden monitorear constantemente parámetros como temperatura, vibración, presión y consumo de energía. Estos datos se transmiten a sistemas centralizados para su análisis inmediato.
El análisis de datos en tiempo real permite:
- Detección instantánea de anomalías en el rendimiento de los equipos
- Predicción más precisa de fallos inminentes
- Ajuste dinámico de los programas de mantenimiento basado en condiciones reales
- Optimización continua de los parámetros operativos para maximizar la eficiencia
Por ejemplo, una planta química podría utilizar sensores IoT para monitorear la presión y temperatura en reactores críticos. Cualquier desviación de los parámetros normales podría desencadenar alertas inmediatas, permitiendo intervenciones preventivas antes de que ocurran fallos costosos o peligrosos.
Aplicación de inteligencia artificial para predicción de fallos
La inteligencia artificial (IA) y el aprendizaje automático están llevando la predicción de fallos a un nuevo nivel. Estos sistemas pueden analizar vastas cantidades de datos históricos y en tiempo real para identificar patrones sutiles que podrían indicar un fallo inminente, incluso antes de que sean evidentes para los técnicos humanos.
Las aplicaciones de IA en mantenimiento predictivo incluyen:
- Modelos de aprendizaje profundo que pueden predecir fallos con semanas o meses de antelación
- Sistemas de recomendación que sugieren acciones de mantenimiento óptimas basadas en múltiples factores
- Análisis de causa raíz automatizado para identificar los orígenes de problemas recurrentes
- Optimización de inventario de repuestos basada en predicciones de fallo
Un ejemplo práctico sería una aerolínea utilizando IA para analizar datos de vuelo y mantenimiento de su flota. El sistema podría predecir cuándo un componente específico de un avión está en riesgo de fallo, permitiendo su reemplazo durante el próximo mantenimiento programado, evitando así costosas cancelaciones de vuelos.
Mantenimiento remoto y realidad aumentada en diagnósticos
La realidad aumentada (RA) está emergiendo como una herramienta poderosa para el mantenimiento remoto y el diagnóstico de problemas. Esta tecnología permite a los técnicos in situ recibir orientación visual en tiempo real de expertos remotos, mejorando la precisión y velocidad de las reparaciones.
Las ventajas del mantenimiento remoto y la RA incluyen:
- Reducción de los tiempos de inactividad al permitir diagnósticos y reparaciones más rápidos
- Acceso instantáneo a experiencia especializada, independientemente de la ubicación geográfica
- Mejora en la precisión de las reparaciones al proporcionar instrucciones visuales paso a paso
- Disminución de los costos de viaje y logística asociados con el envío de expertos a sitios remotos
Imagine un técnico en una plataforma petrolera offshore utilizando gafas de RA para recibir orientación visual de un especialista ubicado a miles de kilómetros de distancia. El experto puede "ver" lo que el técnico ve y proporcionar instrucciones precisas, superponiendo diagramas y marcadores en la vista del técnico para guiar la reparación.